Driving Operational Excellence in Manufacturing
Our Mission
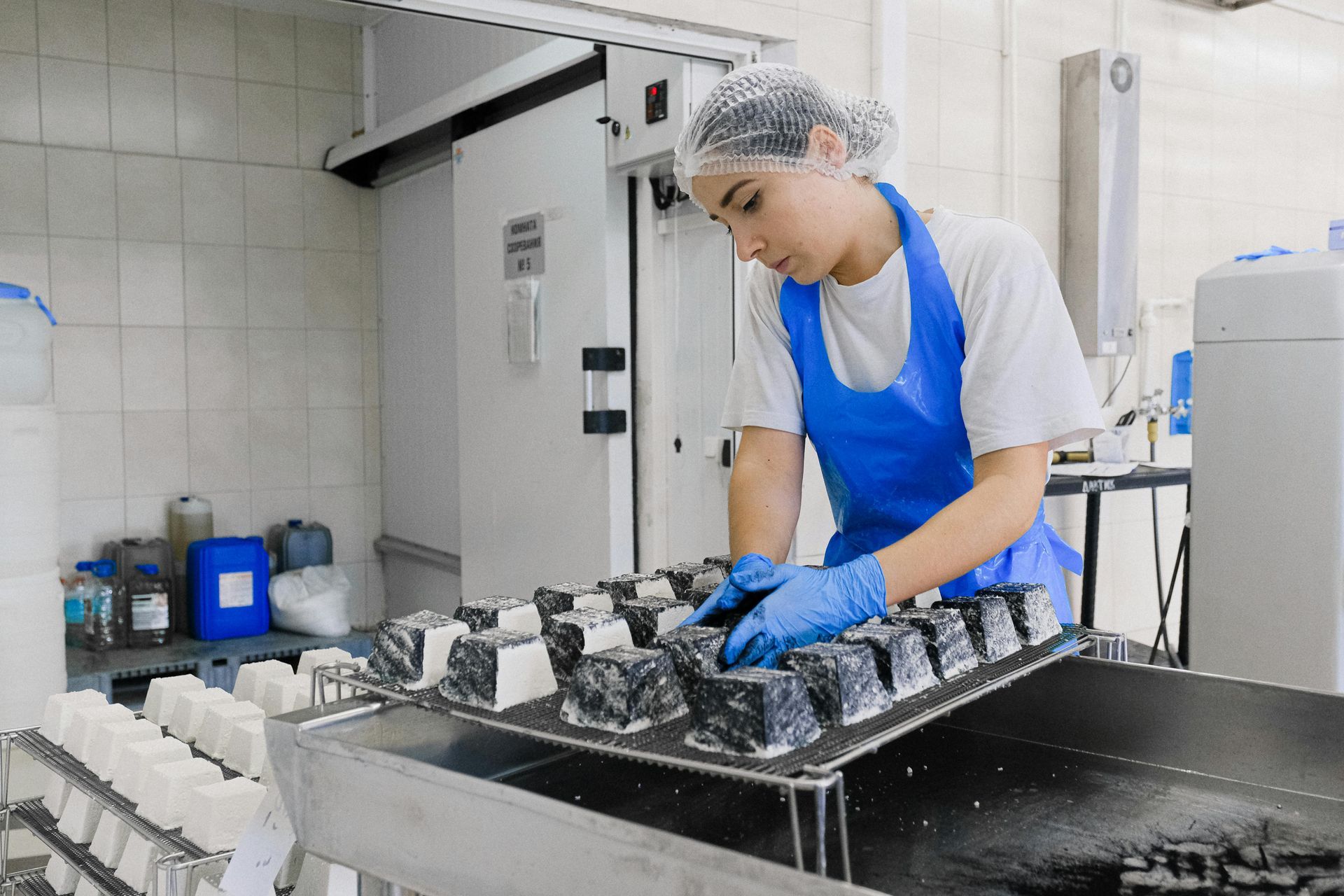
Expert Guidance Rooted in Experience
Unlocking Capacity and Efficiency
Bridging Strategy and Execution
Solving Complex Operational Challenges
Enhancing Free Cash Flow and Reducing Costs
Navigating High-Stakes Environments
Partnering for Sustainable Growth
Committed to American Manufacturing Excellence
Insights on Operations
Latest Trends and Challenges in Operations Management
Supply Chain Resilience
Lean Manufacturing
Digital Transformation
Workforce Optimization
Sustainability Practices
Risk Management
Automation Integration
Cost Reduction Strategies
Quality Control Advances
Challenges in U.S. Manufacturing
- Labor Shortages & Skills Gap
U.S. manufacturing continues to face a critical shortage of skilled workers. With an aging workforce and fewer young people entering trades, leadership must invest heavily in recruiting, training, and upskilling. The challenge isn’t just hiring—it’s developing the next generation of leaders and technicians who can thrive in high-tech, fast-moving environments. - Leadership Pipeline & Organizational Agility
Beyond operations, there’s a leadership challenge: succession planning, change management, and building agile teams that can adapt quickly to disruption. Strong middle management and cross-functional collaboration are more important than ever. - Rising Costs & Margin Pressure
Inflation, rising wages, energy costs, and material volatility are squeezing margins. Manufacturing leaders must balance cost control with long-term investment in technology, talent, and infrastructure—all while maintaining product quality and delivery performance. - Supply Chain Disruptions
Ongoing global instability, geopolitical tensions, and transportation delays are making supply chains less predictable. U.S. leaders are increasingly challenged to localize sourcing, build supplier diversity, and invest in real-time visibility tools—all while managing customer expectations. - Cybersecurity Risks
As operations become more digital, they're also more vulnerable. Ransomware and cyberattacks targeting manufacturers have surged, putting sensitive data and production uptime at risk. Strong leadership is needed to prioritize IT/OT security, employee training, and crisis preparedness. - Sustainability & Regulatory Complexity
ESG pressures, decarbonization goals, and tightening regulations require manufacturers to rethink operations—from raw materials to energy usage and waste management. Leadership must align sustainability with profitability, often without clear ROI in the short term. - Reshoring & Investment Strategy
While reshoring presents a strategic opportunity, it comes with high capital requirements and complexity. Leaders are tasked with making long-term investment decisions in capacity, automation, and location strategy amid shifting government policies and uncertain demand.
In short, U.S. manufacturing leaders today must be both strategic and hands-on—balancing technology, talent, resilience, and transformation in one of the most demanding industrial environments in decades.
manufacturing Metrics to drive Operational excellence
Overall Operational
- OEE (Overall Equipment Effectiveness) = Availability × Performance × Quality
- Throughput – Number of units produced over a specific time period
- Cycle Time – Time to complete one production cycle
- Takt Time – Rate at which a product needs to be completed to meet customer demand
- Capacity Utilization – % of total production capacity being used
- Downtime – Total or unplanned machine downtime
Production Efficiency
- First Pass Yield (FPY) – % of units that meet quality standards without rework
- Scrap Rate – % of materials or products discarded during production
- Rework Rate – % of units requiring rework
- Changeover Time – Time to switch from one product or process to another
- Labor Productivity – Output per labor hour or employee
Inventory & Fulfillment
- Inventory Turnover – How often inventory is sold and replaced
- Days of Inventory (DOI) – Average number of days inventory is held
- On-Time Delivery – % of orders delivered by promised date
- Order Fulfillment Lead Time – Average time from order to delivery
- Perfect Order Rate – % of orders delivered without error (correct quantity, on time, defect-free) Quality KPIs
- Defects Per Million Opportunities (DPMO)
- Cost of Poor Quality (COPQ) – Includes internal & external failure costs
- Customer Complaints – Volume and trends
- Return Rate / RMA Rate – % of products returned by customers
Maintenance
- Mean Time Between Failures (MTBF)
- Mean Time To Repair (MTTR)
- Planned Maintenance % – Ratio of planned to total maintenance
- Maintenance Cost per Unit Produced
Workforce & Safety
- Attendance Rate
- Employee Turnover Rate
- Training Hours per Employee
- Lost Time Injury Frequency Rate (LTIFR)
- Near Miss Reports
- Safety Incidents per Month/Quarter
Financial
- Cost per Unit
- Production Cost Variance
- Operating Margin
- Return on Assets (ROA)
- Budget Adherence (CapEx & OpEx)
Lean & Continuous Improvement
- Kaizen Events Completed
- Suggestions Implemented
- Value Stream Lead Time
- 5S Audit Scores
- Waste Reduction (by type: time, motion, inventory, etc.)
Frequently Asked Questions
What industries do you specialize in?
How do you approach operational challenges?
What is your client engagement process?
Can you assist with labor negotiations and contract management?
Expertise
John Mitchell
With over 30 years in automotive and aerospace manufacturing, John specializes in operational turnarounds and capacity optimization, delivering measurable improvements in efficiency and cost control.
Background
Experience
Sarah Lee brings deep knowledge in precision machining and supply chain management, having led multi-plant operations and negotiated complex labor agreements to enhance productivity.
Focus
David Ramirez
David’s expertise lies in large-scale fulfillment and industrial manufacturing, driving growth through strategic planning and hands-on leadership in capital-intensive program launches.
Approach
Our consultants combine tactical execution with strategic insight, addressing systemic challenges to unlock sustainable operational improvements tailored to each client’s unique needs.
Team
Snapshots of operational excellence in action
Operations Consulting
Visual highlights from projects driving manufacturing transformation