7 TYPES OF WASTE
7 Types of waste in manufacturing
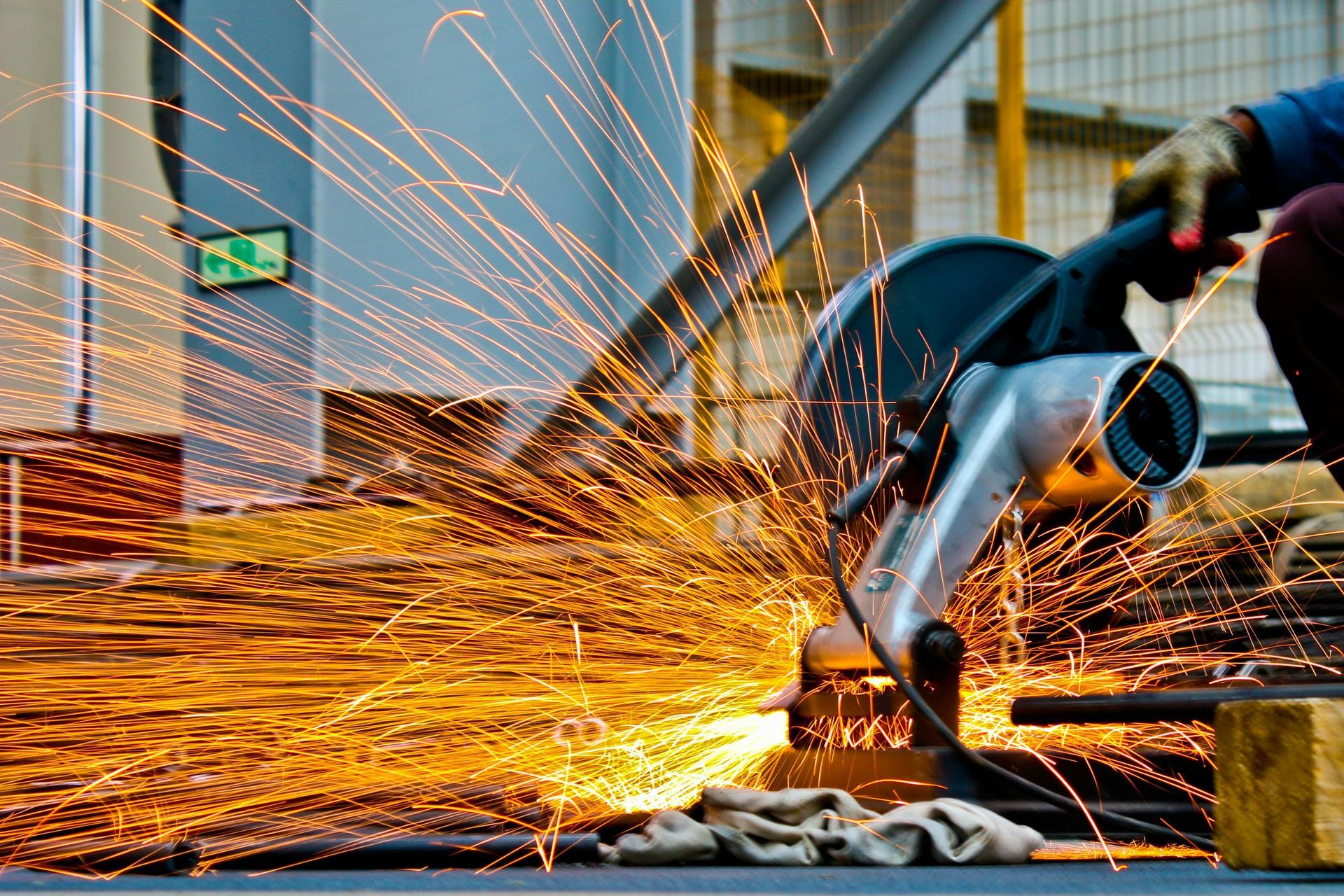
The 7 Types of Waste in Lean Manufacturing:
What They Are and Why They Matter
In Lean manufacturing and operational excellence, waste is anything that does not add value to the customer. By identifying and eliminating these non-value-adding activities, companies can increase efficiency, reduce costs, and improve quality.
The concept of the 7 types of waste, or "7 Muda", originated from the Toyota Production System (TPS), and it remains a cornerstone of Lean thinking today.
🚧 1. Overproduction
Definition: Producing more than is needed or producing it before it's needed.
Why it’s a problem:
- Leads to excess inventory
- Increases storage costs
- Hides other process inefficiencies
Example: Making 1,000 units when only 500 are ordered.
📦 2. Inventory
Definition: Excess raw materials, work-in-progress (WIP), or finished goods.
Why it’s a problem:
- Ties up capital
- Hides defects
- Takes up space
Example: A warehouse full of unsold product due to inaccurate demand forecasting.
🚶 3. Motion
Definition: Unnecessary movement by people (not to be confused with transportation).
Why it’s a problem:
- Wastes energy and time
- Increases ergonomic risks
- Adds no value to the product
Example: A worker walking back and forth across a shop floor due to poor layout.
🚚 4. Transportation
Definition: Unnecessary movement of products or materials.
Why it’s a problem:
- Adds cost without adding value
- Increases risk of damage
- Slows down lead time
Example: Moving parts between multiple facilities during production.
⏱️ 5. Waiting
Definition: Idle time when people or machines are waiting for something to happen.
Why it’s a problem:
- Reduces productivity
- Increases lead times
- Causes bottlenecks
Example: A machine operator waiting for maintenance or instructions.
🔁 6. Overprocessing
Definition: Doing more work or using more expensive materials than necessary.
Why it’s a problem:
- Increases cost and cycle time
- Can confuse or frustrate the customer
- May require rework
Example: Using a laser cutter when a simple blade would suffice.
❌ 7. Defects
Definition: Products or services that don’t meet quality standards and require rework or disposal.
Why it’s a problem:
- Directly impacts customer satisfaction
- Leads to rework, waste of materials, or scrap
- Damages brand reputation
Example: A part that fails quality inspection and must be re-manufactured.
🔧 More from Gemba Academy on the 7 Wastes
🎯 Summary Table: The 7 Wastes
Waste TypeKey IssueExampleOverproductionProducing too much, too soonMaking extra units before demandInventoryStockpiling parts or materialsExcess warehouse inventoryMotionUnnecessary movement of peopleWalking between distant toolsTransportationMoving items unnecessarilyShipping between multiple plantsWaitingIdle time or delaysWaiting for approvals or partsOverprocessingDoing more than neededOverengineering a productDefectsErrors that require correctionScrapped items from bad machining
🛠️ Next Steps: Eliminating Waste
- Map your value stream to identify non-value-adding steps.
- Engage employees to observe where inefficiencies occur.
- Standardize processes and simplify wherever possible.
For a deeper dive, consider reading:
📘
Lean Thinking by James P. Womack and Daniel T. Jones
✅ Final Thoughts
Understanding and eliminating the 7 wastes is key to creating a more efficient, agile, and profitable operation. When you focus on value from the customer’s perspective, cutting waste becomes a daily mindset—not just a one-time effort.