Lean meeting infrastructure for manufacturing operations
Lean communication process for a manufacturing operation
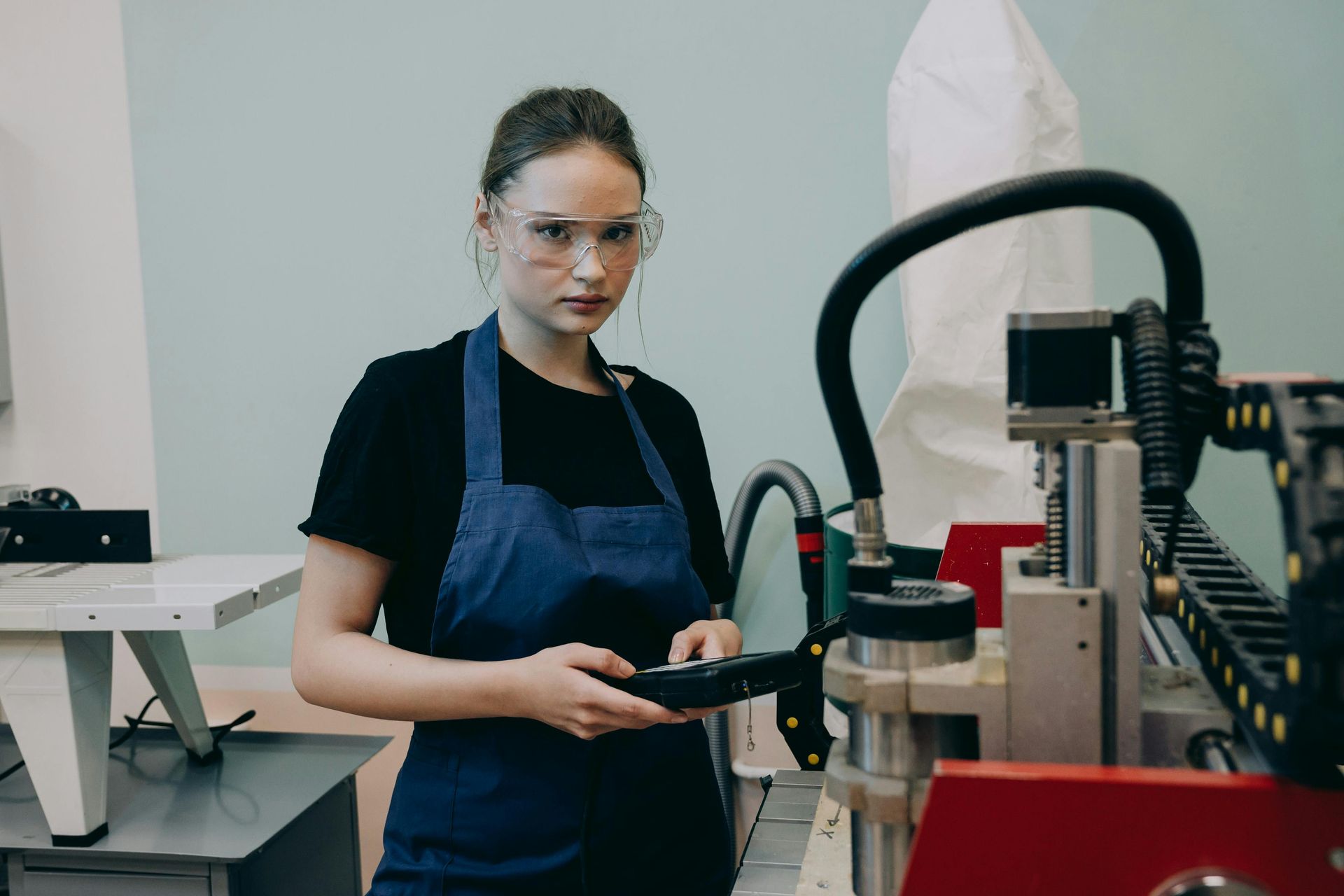
An efficient and lean meeting and communication process is essential in a manufacturing plant to ensure alignment, reduce waste, and drive continuous improvement.
It creates a structured yet flexible environment where information flows clearly across departments and levels. Below are the required components:
I. Leadership review meeting (Staff meeting) is a strategic, less tactical, session focused on operational alignment and follow up. The meeting is cross functional including: Operations, Sales, Maintenance, Quality, Finance, Engineering, HR, Purchasing and Supply Chain teams. Each Staff lead should report KPI updates for their areas. Run charts are best for trends. The team should also review longer term goals and objectives and keep a live action tracker. Assign virtual folder where staff leaders put presentation material ahead of meeting. Working lunch is a nice touch! Team will look forward to attending a bit more. Efficiency is the key. Frequency: Bi-monthly, Duration: 2 hours.
KPI trend reviews provide a data-driven foundation for managing performance and identifying areas needing attention. Communication should be exception based focusing on deviations from standards to reduce noise and enhance decision-making speed.
II. Continuous improvement meetings with key plant disciplines represented. Project champions should provide update. Start with one improvement idea per person and grow from there. Keep one central repository as CI tracker. Make it so everyone can access and edit. Always keep it positive and encouraging. Invite diverse perspectives and break down silos, creating opportunities for sustainable change. Frequency: Bi-monthly, Duration: 1 hour
Talk with the operators performing the processes, they'll tell you where the opportunities are hidden. CI should be both top down and bottoms up. People who run the equipment and are closest to the process and should be actively engaged.
III. Gemba walks with the staff. Have a common starting point at the same time every week. Invite the staff as well as others that make sense to join. Visit an area that is a success story where recent improvements have been made then visit an area that the team agrees is an opportunity for improvement, each week. Keep notes and follow up. Attached link is a good summary on how to run an effective Gemba walk:
https://www.twi-institute.com/gemba-walk/
Frequency: Weekly, Duration: 1 hour
IV. Morning Start up meeting. Cross functional "huddle" to review previous day production cycle KPI's, priorities for the day, exceptions, schedule, not intended for deep dives (however use it as a catalyst for sidebars later) Frequency: Daily, Duration: 30 minutes.
V. Scheduling meetings further ensure proper coordination of production flow, materials, and workforce planning. Together, these communication tenants foster a culture of accountability, engagement, and lean thinking throughout the organization. Frequency: weekly, Duration: 30 minutes
VI. Plant All-Hands meetings. This is an opportunity to share the business with the workforce. Topics such as schedules, new business wins, plant KPI's, industry updates, upcoming events, new investments and other. Always leave time at the end for Q&A. This is necessary and healthy part of the meeting. Keep track of issue brought up and provide updates at subsequent meetings. Frequency: Quarterly, Duration: 30 minutes
These six meetings support the 4 pillars of TPS. Support the operators, continuously improve, attack waste in the enterprise and standardize as much as possible.
Approach this with discipline and rigor. It promotes a well informed, proactive team capable of tackling multiple challenges that manufacturing operations face today.
Anticipate some resistance. In the absence of an efficient meeting process, teams gravitate to reactive behavior, which usually requires less structure and organization. Nevertheless, the tone is set by Plant Leadership. If you decide to implement this structure, DO NOT waiver or cancel meetings due to daily fires.
Link referencing strategies for lean meetings: https://www.lean.org/the-lean-post/articles/6-ways-to-lay-the-groundwork-for-more-effective-meetings/